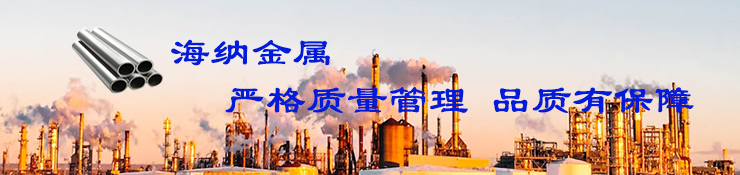
薄壁钛管制造技术的难点
薄壁钛管因具备重量轻、比强度高的特性,在航空航天、医疗器械等高端领域需求显著。然而,其制造过程面临诸多技术挑战,制约着产品质量与生产效率的提升。
成型难度大是首要难题。钛合金变形抗力高、塑性变形范围窄,在薄壁管冷轧或冷拔过程中,管材极易因受力不均产生局部失稳,导致管壁厚度偏差大、圆度超差。同时,钛合金回弹现象明显,精确控制管材尺寸精度极为困难,对模具设计、加工设备的精度及工艺参数匹配性要求极高。
表面质量控制难。薄壁钛管壁厚较薄,在成型过程中,管材与模具之间的摩擦力易造成表面划伤、擦伤等缺陷。此外,钛合金化学活性高,在高温下易与模具材料发生粘连,进一步恶化表面质量。而表面微小缺陷可能成为应力集中点,降低管材的疲劳性能和耐腐蚀性能,难以满足高端应用场景的严苛要求。
内部组织与性能均匀性不易保证。钛合金在加工过程中,由于变形不均匀,易导致管材内部组织出现晶粒大小不均、残余应力分布不均等问题。尤其是在薄壁管材中,局部变形过大可能引发组织纤维化或织构异常,影响管材的综合力学性能,使得不同部位的强度、韧性存在差异,增加产品失效风险。
焊接工艺复杂。对于需要焊接成型的薄壁钛管,焊接过程中极易出现烧穿、变形等问题。钛合金熔点高,热导率低,焊接时热量不易散失,易造成局部过热;同时,钛在高温下化学活性极高,易与空气中的氧、氮等元素发生反应,导致焊缝脆化。如何在保证焊接质量的同时,控制焊接变形,成为薄壁钛管制造中的关键技术瓶颈。
上一篇:钛管在石油开采设备中的创新应用下一篇:没有了
相关文章:
暂无相关文章